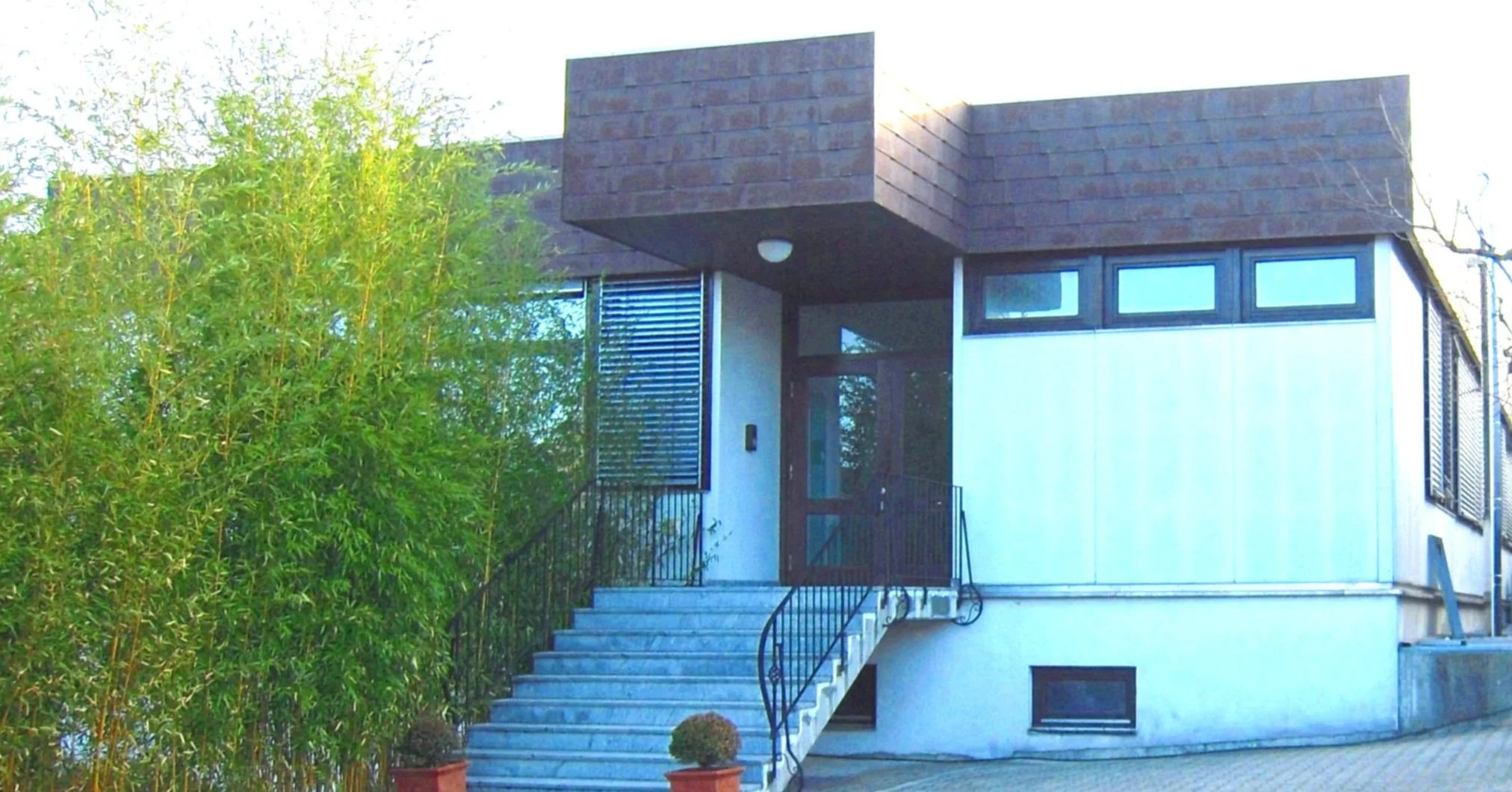
Die Drechsel GmbH
Leiterplatten sind das wichtigste Verbindungselement zwischen mikroelektronischen Bausteinen. Wir sehen sie zwar nie, ohne sie jedoch ist ein Mobiltelefon nur ein Stück Plastik.
Wie kaum eine andere Branche durchdringt die Mikroelektronik das gesamte Wirtschaftsleben und ist der Innovationsmotor für alle Bereiche, in denen Elektronik im Spiel ist. Die Entwicklung geht dabei in Richtung immer kleinerer Baugruppen mit immer größerer Leistungsfähigkeit. Was heute technisch noch unvorstellbar ist, wird zukünftig in Serie produziert.
Die wichtigsten Abnehmer dieser High-Tech Baugruppen sind die Hersteller der Informations- und Kommunikationstechnik, die Luft- und Raumfahrtindustrie, die Automobilindustrie, die Medizintechnik, die Verkehrstechnik und der Maschinenbau.
Die Leiterplatte mit ihren immer kleineren und feineren Strukturen bei zunehmenden Packungsdichten hat mit den Bauteilen aus den Anfängen der Leiterplattentechnik nur noch den Namen gemein.
Als Ersatz für die „Kabelbäume" setzte sich in den fünfziger Jahren die „Gedruckte Schaltung" durch. Die einseitig mit Kupfer beschichtete Platte bestand aus mit Phenolharz getränktem Hartpapier. Auf ihr wurden die elektrischen und mechanischen Strukturen meist von Hand aufgebracht. Ende der sechziger Jahre ermöglichte die doppelseitige Kupferbeschichtung erstmals komplexere Verdrahtungen. Seit dieser Zeit treiben wir als mittelständischer Hersteller die Entwicklung unseres Produktes aktiv voran. Und seit der Firmengründung im Jahr 1969 verstehen wir uns nicht nur als reiner Fertigungsbetrieb, sondern als beratender Partner unserer Kunden.
Die Anwendungsgebiete für Leiterplatten „Made by Drechsel" sind so unterschiedlich wie die Anforderungen unserer Kunden. Ob Multilayer, SMD-Boards /Surface Mount Device), CSP (Chip Size Packages), Chip-on-board-Technik oder Flip-Chip-Technik. Wir sind aufgrund unseres Know-hows, unserer Flexibilität und unserer Erfahrung in der Lage, fast jeden Kundenanspruch zu erfüllen.
Unsere Firmen-Philosophie
Die Anforderungen an die Leiterplatte und die Produktionstechnik haben sich seit der Gründung unseres Unternehmens stark verändert. Unverändert dagegen ist noch immer unsere Arbeitsweise: Gemeinsam mit unseren Ansprechpartnern suchen wir die optimale Lösung für ihre Leiterplatte, die wir dann mit modernster Technik fertigen und pünktlich, zu einem für alle Beteiligten attraktiven Preis-Leistungsverhältnis liefern.
Unsere Leistungen erbringen wir deutschlandweit für Kunden in den Branchen Automobilindustrie, Kommunikationstechnik, Luft- und Raumfahrttechnik, Mess- und Regeltechnik, Medizintechnik, Hochfrequenz- und Mikrowellentechnik und Sensortechnik. Aufgrund unserer Organisationsstruktur und unserer technischen Ausstattung haben wir uns in über fünfzig Jahren den Ruf als äußerst reaktionsschneller, flexibler, kreativer und zuverlässiger Partner rund um das High-Tech Produkt Leiterplatte erarbeitet.
Persönliche Beratung
Als mittelständischer Hersteller machen wir seit Jahren die Erfahrung, dass unsere Kunden vor allem die persönliche Beratung durch qualifizierte Ansprechpartner erwarten, wenn sie einen zuverlässigen Leiterplatten-Partner suchen. Durch gezielte Weiterbildungsmassnahmen, speziell in der Datenverarbeitungs- und Fertigungstechnik, stellen wir sicher, daß unsere Mitarbeiterinnen und Mitarbeiter stets für die neuesten Entwicklungen gerüstet sind. Unsere Produktion haben wir in den letzten Jahren in allen Bereichen auf den technisch neuesten Stand gebracht und werden dies auch in Zukunft tun.
Bei der Suche nach der technisch und wirtschaftlich optimalen Lösung setzen wir schon in der Entwurfsphase auf eine intensive Zusammenarbeit zwischen unseren Spezialisten und den Profis auf der Kundenseite, vorwiegend den Ingenieuren und Technikern aus der Entwicklung. Steht der Entwurf und sind alle Beteiligten damit zufrieden, sorgen wir mit einem straffen Kosten-und Zeitmanagement dafür, daß die qualitativ hochwertige Leiterplatte zu einem vernünftigen Preis gefertigt wird. Dabei kann es durchaus vorkommen, daß wir unseren Kunden ein optimiertes Schaltungslayout vorschlagen, mit dem ein technisch oder wirtschaftlich besserer Produktionsablauf möglich wird. Mit Hilfe unserer integrierten Produktionsplanung und -steuerung (PPS) können wir gewährleisten, dass unsere Produkte nicht nur qualitativ hochwertig, sondern auch pünktlich unser Werk verlassen.
Expertise in Mechanik, Foto-,Galvano- und Oberflächentechnik
Der Trend in der Elektronik führt zu immer kleineren und leistungsfähigeren Geräten, von denen ein Maximum an Zuverlässigkeit erwartet wird. Notebooks, Mobiltelefone, Armbanduhren mit GPS, medizinische Geräte: Die Reihe dieser Miniaturisierungsbeispiele lässt sich beliebig fortsetzen.
Die Forderung an die Leiterplattenhersteller sind eindeutig: mehr I/Os pro Bauteil, steigende Verdrahtungsdichte, mehr Lagen, mehr Durchkontaktierungen auf kleinstem Raum. In unserer Mechanik begegnen wir diesen Anforderungen mit CNC-gesteuerten High-End-Bohr- und Fräsautomaten, die maximale Wiederholgenauigkeiten bei minimaler Toleranz garantieren. Z-Achsen-kontrollierte Mikrobohrungen im Bereich von 150 µm Durchmesser als Durchbohrungen, Sackbohrungen und Buried Vias gehören für unsere Mechanik zum Tagesgeschäft.
Um den Anforderungen unserer Kunden an den Aufbau ihrer Leiterplatten noch besser gerecht zu werden, haben wir auch im Bereich Fototechnik kräftig investiert. Schliesslich sind perfekte Leiterbilder und Lötstopmasken die Grundlage für eine fehlerlose Funktionsfähigkeit. Dank moderner LDI-Technologie sind wir heute in der Lage, ohne zeitliche Verzögerung komplexe Feinststrukturen zu produzieren.
Jeder Kunde erwartet von seinem Zulieferpartner eine individuelle, qualitativ hochwertige und fehlerlose Problemlösung. Wir sind da nicht anders und suchten lange, bevor wir uns schließlich entschieden haben, unsere neue Galvanikanlage selbst zu entwickeln und umzusetzen. Nur so konnten wir sicher sein, in Zukunft Leiterplatten mit einem Galvanoautomaten produzieren zu können, der optimal auf unsere Bedürfnisse zugeschnitten ist. Mit dieser Anlage lassen sich kleine Losgrößen, die ständiges Umrüsten erfordern, ebenso rationell und sicher fertigen wie echte Grossserien.
Höchste Flexibilität bei vollautomatischem Ablauf garantiert der Einsatz modernster Steuerungstechnik, bei der jedes Warengestell mit einem mobilen Datenspeicher ausgerüstet ist. Vor dem Eintritt in die entsprechende Prozessstufe werden die relevanten Daten in die Automatensteuerung eingelesen, wodurch praktisch jede Leiterplatte in unserer Galvanik individuell bearbeitet wird.
Ob eine elektronische Baugruppe funktioniert oder nicht, hängt hauptsächlich von der Leiterplatte ab, die darin ihren Dienst tut. Bei den heutigen und zukünftigen Anforderungen an unser Produkt ist die absolut planare Oberfläche deshalb ein Muss. Dies gilt besonders bei Techniken wie SMD, Chip-on-board, Flip Chip oder BGA (ball-grid-array) und wir messen dem Oberflächenfinish einen entsprechend großen Stellenwert bei. Da die Suche nach der idealen und universellen Oberflächentechnik bis heute erfolglos bleibt, bieten wir unseren Kunden - je nach Anforderung, Fertigungsstrategie und späterem Einsatzgebiet - verschiedene Verfahren zur Oberflächenveredelung an. Neben der zuverlässigen und wirtschaftlichen partiellen Heissluftverzinnung (Hot Air Levelling - HAL) sind dies galvanisch Nickel/Gold, chemisch Zinn oder chemisch Nickel/Gold.
Qualitätsversprechen
Kreativität, Flexibilität, Zuverlässigkeit und Qualität nennen wir als wichtige Merkmale unserer Arbeit, deren Beurteilung wir letzten Endes aber unseren Kunden überlassen. Um unseren eigenen und den Qualitätsansprüchen des Marktes gerecht zu werden, haben wir ein DEKRA-zertifiziertes Qualitätssicherungssystem auf der Basis der Normvorschriften der DIN/ISO 9001, sowie die UL-Zulassung aus den USA. Unsere Mitarbeiterinnen und Mitarbeiter sind sich bewusst, dass von der Qualität und Funktionsfähigkeit unserer Produkte alles abhängt und handeln entsprechend. Regelmäßige metallurgische und chemische Kontrollen sind ebenso selbstverständlich wie die Schichtdickenkontrolle zur ständigen Überwachung der galvanisch aufgebauten Metallschichten. Neben regelmäßigen optischen Kontrollen steht am Ende des Produktionsprozesses schliesslich die elektrische Prüfung, bevor die Leiterplatte per Kurier oder persönlich ausgeliefert wird.
Verpflichtung zum Umweltschutz
Als Unternehmen einer sehr energie- und ressourcenintensiven Branche wissen wir um unsere Verantwortung gegenüber der Gesellschaft und der Umwelt, in der wir leben. Lösungsmittelfreie Techniken und Recyclingverfahren sind daher bei uns seit Jahrzehnten Standard. Neue Produktionsverfahren und Fertigungsanlagen prüfen wir grundsätzlich auf ihre Umweltverträglichkeit, bevor wir sie in Betrieb nehmen. Wir haben dabei die Erfahrung gemacht, dass umweltverträgliche Verfahren zur Senkung der Fertigungskosten beitragen.